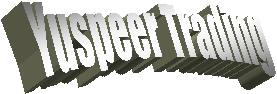
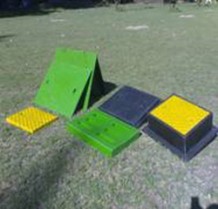
The benefits of polymer manhole covers and frames
1. Tested to SABS standard (1882), test report available
2. Test equipment calibrated by the SABS
3. Up to 47% cheaper than cast iron
4. Our product is not stolen like cast iron or any metallic product
5. Grip, non slip surface
6. Country wide delivery
7. No rust like any metal
8. No painting required, no maintenance
9. We stock a full range from circles to rectangles to squares to gratings and much more
10. Used by big construction companies and most municipalities
11. Carries a weight of up to 13,5 tonnes
12. We supply on convenient terms
13. We carry stock
14. Lighter than cast iron, without compromising its performance
15. Easier to handle, due to lighter weight
16. More than six times stronger than ordinary concrete.
On a daily basis across the length and breadth of South Africa,
manhole covers are being stolen and sold as scrap metal. Pick
up a newspaper most days of the week, and you will find at
least one story of a car driving into an open manhole or a person stepping
into one. Damage to cars can run into many thousands of rands
and injuries to people can be fatal or, at the very least, crippling. The
reasons for manhole cover theft are actually quite simple – poverty,
survival and greed. A cast iron manhole cover is quoted to fetch up to
R500 at the local scrap dealer. And, with the price of steel rising by the
day, stealing cast iron manhole covers is a fast way to make a quick
buck for unscrupulous scrap metal dealers.
Survey
In a survey carried out by a few manhole cover suppliers and users,
it was found, in the four biggest municipalities in South Africa, that
there is a total of 61 832 manhole covers missing, all presumed
stolen. The problem is not only affecting big metros but also the
Manhole theft: a solution
smallest of towns. Legal claims and lawsuits are being lodged against
municipalities for property damage and personal injury caused by
open manholes.
Polymer concrete manhole covers
There is, however, good news. Polymer concrete manhole covers have
no scrap value. They have been around since 1992 and have been
widely used in the
ever since. Slowly, Polymer concrete manhole covers are making
inroads into the rest of South Africa and abroad due to their price
competitiveness and proven track record. A Polymer concrete manhole
cover would cost the user about 40% less than a similar manhole
made from cast iron. The cost advantage alone allows the user to get
more manhole covers for their money and thereby enables a quicker
solution to solving the backlog of open manholes.
Technology
Polymer concrete was developed in Germany in the early 50s and has
been widely used in many different applications. The application was
tried on manhole covers and, with some adjustments to the initial
design, polymer concrete could be safely applied to manhole covers.
Polymer concrete manhole covers are made from a composite material
that is bound together by resin and fibreglass.
The South African Bureau of Standards (SABS)
The South African Bureau of Standards (SABS) has formally published
a standard, SANS 1882 of 2003, to recognise the need for an alternative
to cast iron and concrete and to give municipalities a better choice
in products to cater for their special, social and public needs. The City
of Cape Town has indicated that the standard on Polymer concrete
manhole covers and frames should be made a compulsory specification
so as to ensure continued excellence in the industry. According to the
Department of Trade and Industry should a regulation be introduced,
Missing manhole covers. A person accidentally falling into these
manholes could sustain serious injury
SNIPPETS
Definition
Polymer concrete (PC), or resin concrete, is a concrete that
uses a polymer binder to supplement or replace cement as
a binder. Polymers are made from simple organic molecules
(monomers) that combine to form more complex structures
through a process called polymerisation, hence the term polymers.
Polymer concrete has a density of 2 260 kg/m3 and a
compressive strength of 37 Mpa.
Composition
Polymer concrete is composed of aggregates that include
silica, quartz, granite, limestone, and other high-quality
material. The aggregate must be of good quality, free of
dust and other debris and dry. Failure of these criteria can
reduce the bond strength between the polymer binder and
the aggregate.
Advantages
Advantages of polymer concrete include:
• rapid curing at ambient temperatures
• high tensile, flexural, and compressive strengths
• good adhesion to most surfaces
• good long-term durability with respect to freeze and thaw
cycles
• low permeability to water and aggressive solutions
• good chemical resistance
• good resistance against corrosion
• lightweight
• may be used in regular wood and steel formwork
• may be vibrated to fill voids in forms
• allows use of regular form-release agents.
Polymer concrete may be used for new construction, or
repairing old concrete. The adhesion properties of polymer
concrete allow patching for both polymer and cementious concretes.
The low permeability of polymer concrete allows it to
be used in swimming pools, sewer pipes, drainage channels,
and other structures that contain liquids.
Disadvantages
Polymer concretes also cost significantly more than conventional
concrete.
Some safety issues arise out of the use of polymer concrete.
The monomers can be volatile, combustible, and toxic.
Initiators, which are used as catalysts, are combustible and
harmful to human skin. The promoters and accelerators are
also dangerous.
such technical regulation would
have to be administered by SABS’s regulatory division. public private participation
process would be engaged take into account the comments
of all interested and
affected parties.